Industrial
Overview
We have expanded our longstanding expertise of innovative powder metal solutions in the Automotive industry to our Industrial Markets customers. Our Industrial Markets portfolio consist of all industries outside of automotive, and we have implemented the same unparalleled PM advantages to provide our customers with the most efficient results.
Below you will find the heart of GKN Powder Metallurgy’s Industrial Markets expertise. Browse through our Industrial-specific capabilities and dive into the sub-markets we serve with high-precision powder metal components.
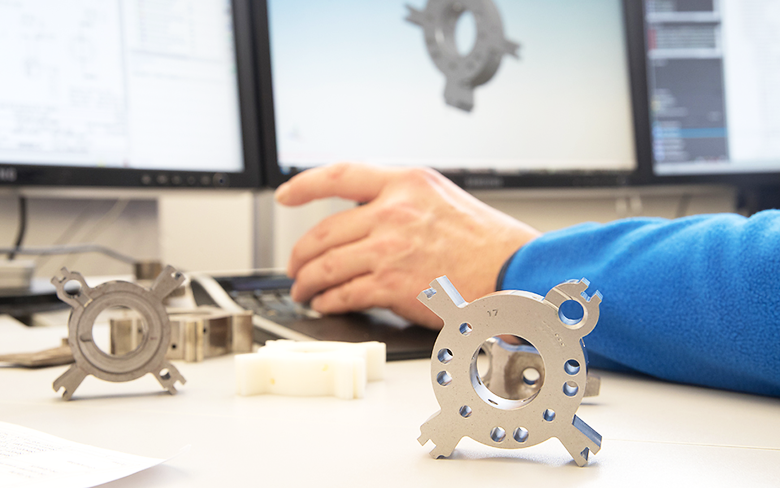
Capabilities
Overview
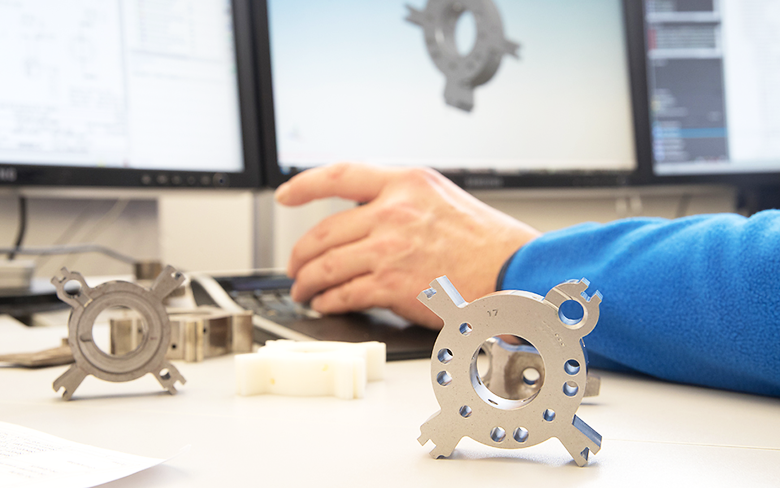
From material properties to advanced press technology and conversions to powder metal, GKN Powder Metallurgy offers a range of capabilities for Industrial applications to solve complex geometry challenges. Our team of experienced engineers will work from concept to production to ensure a tailored powder metal solution.
Materials
GKN Powder Metallurgy is a world leader in the manufacturing of iron and steel powders, and these materials are comparable or exceed wrought steel equivalents. Powder metal technology allows for intelligent alloy design. We also offer unique soft magnetic alloys for electrical applications.
Associated processes:
- Conventional Sintering
- Powder Forging
- Metal Injection Moulding
- Additive Manufacturing
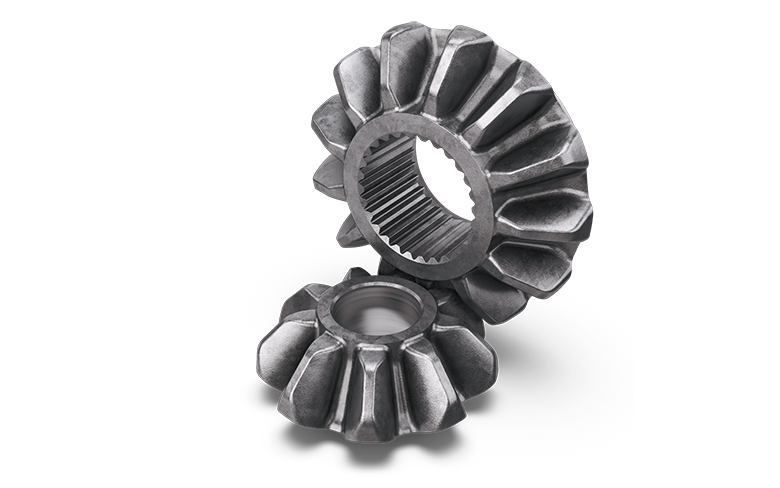
Aluminum is a lightweight material that is 65% lighter than steel. GKN Powder Metallurgy has developed an Aluminum Metal Matrix Composite material that exceeds diecast materials in wear and strength. We are a leader in the use of Aluminum MMCs with four products already in serial production.
Associated processes:
- Conventional Sintering
- Powder Forging
- Additive Manufacturing
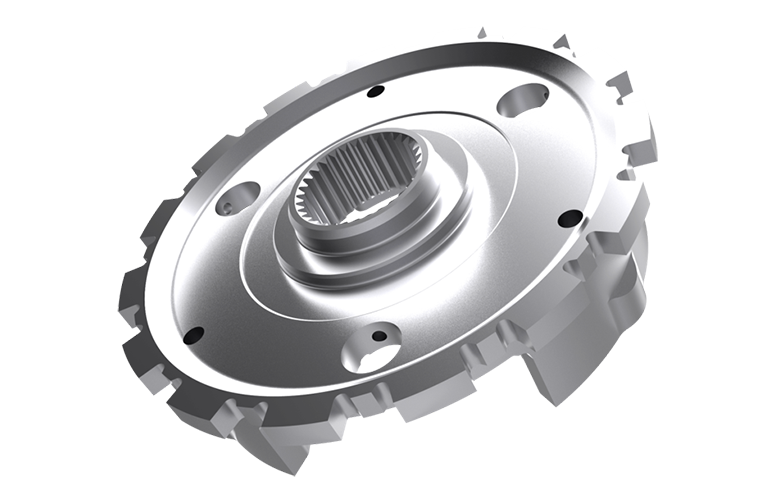
GKN Powder Metallurgy offers a corrosion-resistant steel material. The material has strong thermal resistance characteristics for exhaust components, valve seats, etc. Stainless steel creates unique, net shape products using powder metal technology to its fullest potential.
Associated processes:
- Conventional Sintering
- Metal Injection Moulding
- Additive Manufacturing
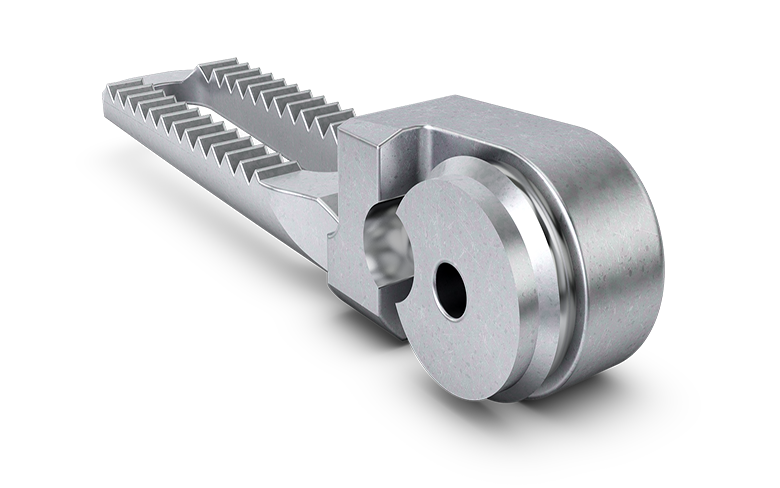
Bronze can fit multiple applications as a multi-functional material with self-lubricating properties. GKN Powder Metallurgy is a leading manufacturer of bronze bushings and bearings.
Associated processes:
- Conventional Sintering
- Metal Injection Moulding
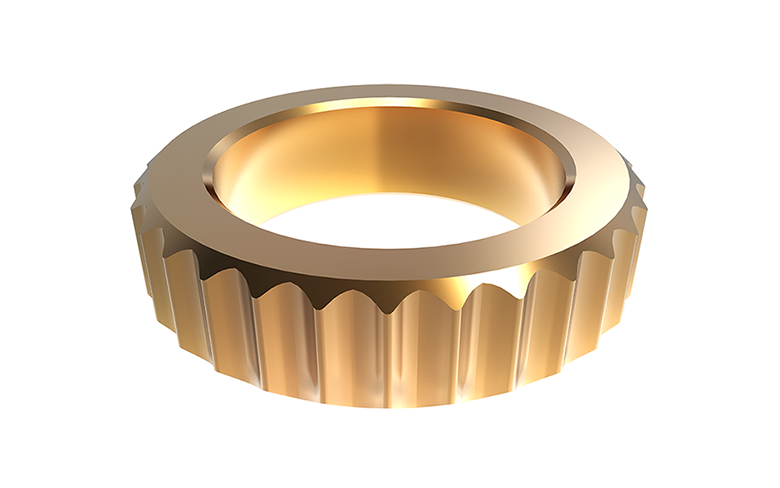
Processes
Delivering the three-dimensional shape capability of plastic injection moulding combined with the performance of alloy steels, stainless steels and high temperature alloys, Metal Injection Moulding (MIM) is uniquely positioned to solve extreme product challenges.
Advantages:
- MIM creates complex geometries at a lower cost in a quicker time frame, compared to traditional processes like milling or casting
- The process allows for creating lightweight products, ideal for compact or mobile applications
- MIM feedstock material has high tensile strength, and tight process controls allow engineers to meet necessary material properties
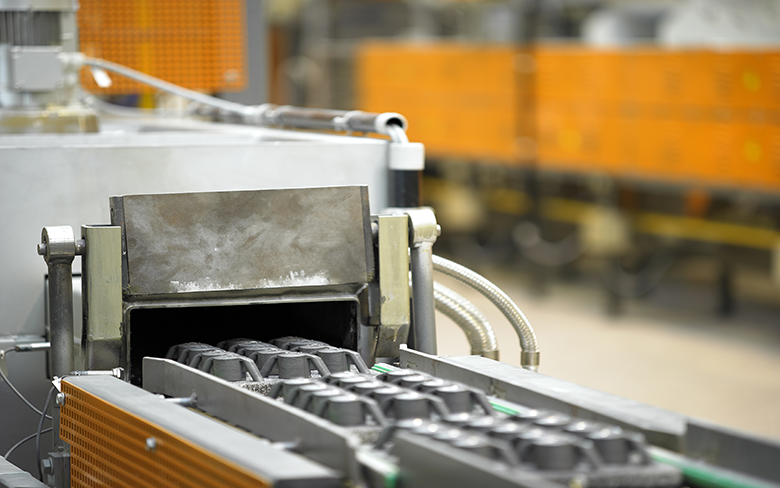
Additive Manufacturing continues to lead the growth opportunities in Industrial markets, by changing the way components are produced. GKN Powder Metallurgy combines its longstanding PM expertise in other markets with advanced 3D printing technology to take on customer's AM opportunities. We offer the widest range of advanced AM technologies and materials, including binder jetting and laser additive manufacturing.
Our AM components are already flying and driving around the world - reducing weight, manufacturing time and cost. To be at the forefront of the industry, GKN has dedicated a global team to advancing AM technology with powder metal technology to become the leader in the Industrial markets.
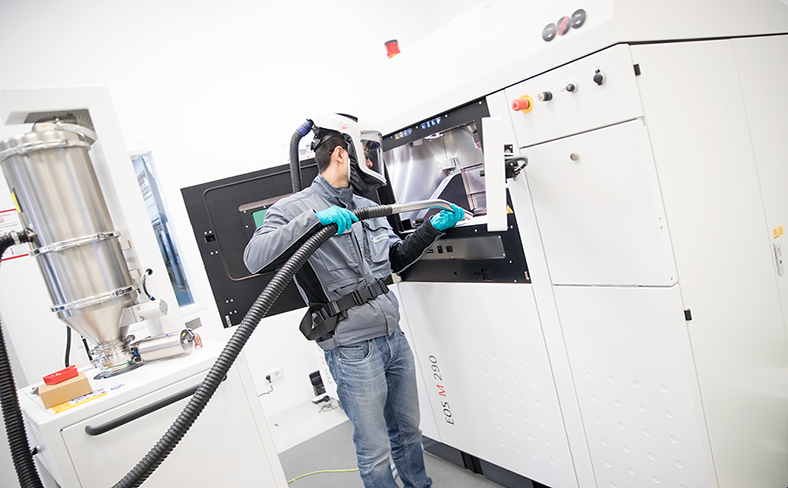
The Forged PM process utilizes clean powder metal alloys, creating optimized designs and a high durability capability. A preform is made by powder compaction and sintering; providing a tailored alloy composition, optimum mass distribution, geometry and near-surface conditions to perfect the flow of material during forging.
Advantages:
- Materials outperform wrought steels by 15 to 30 percent in durability
- Forging provides consistent and repeatable datum features without draft angles and flash lines
- Intelligent preforms allow for components to be produced with a single stroke of the forging press
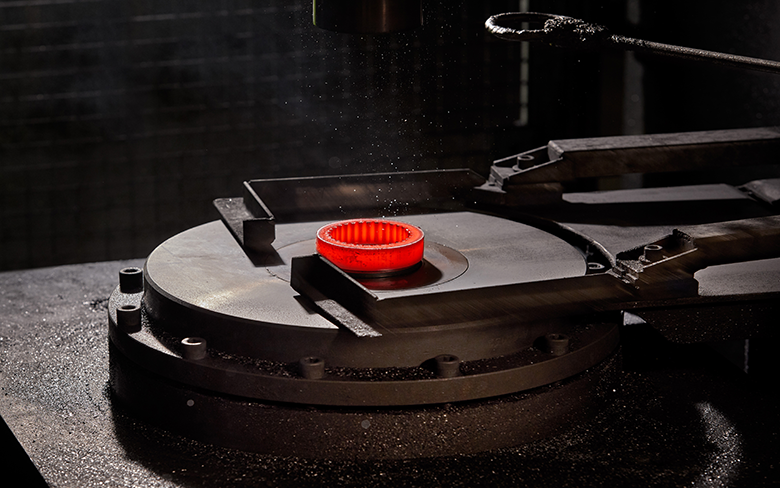
One of the greatest advantages of powder metal technology is the ability to create near net shape components. GKN Powder Metallurgy's Advanced CNC Press Technology provides the opportunity to reduce secondary operations and gives customers greater design flexibility for products.
We leverage our internal tooling design and manufacturing capability to optimize the compaction process. Because of our Advanced CNC Presses, the boundaries for product design expands with high volume production at a lower cost.
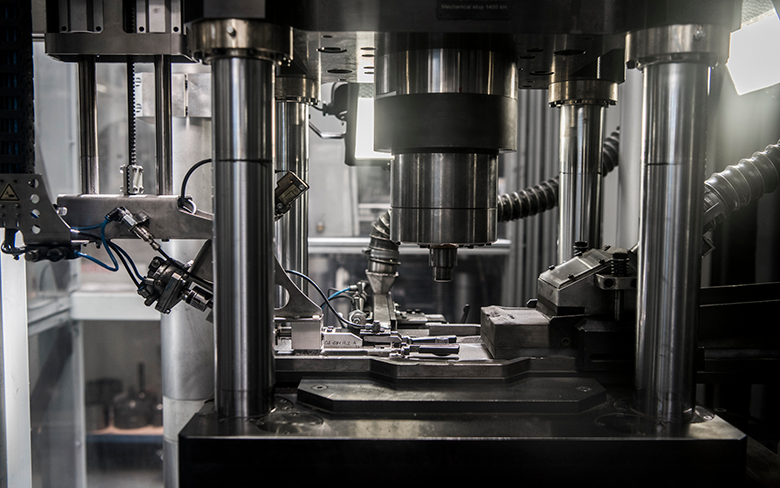
Design for PM
Powder metal technology creates lighter weight and more efficient solutions than traditional technology, but our team of experienced engineers ease the transition from traditional metals to powder metal. GKN Powder Metallurgy uses a tested cycle for converting to powder metal to ensure proper testing and simulation:
- Maximize material properties: We find and test the right material to meet application requirements
- Optimize design: Powder metal allows for complex geometries and designs, typically unavailable elsewhere
- Process selection: We select the right process to produce a part at a lower cost with limited to no secondary machining or additional assembly operations
- Testing and modeling: We ensure the component will withstand any application requirements, by utilizing our in-house testing and analysis.
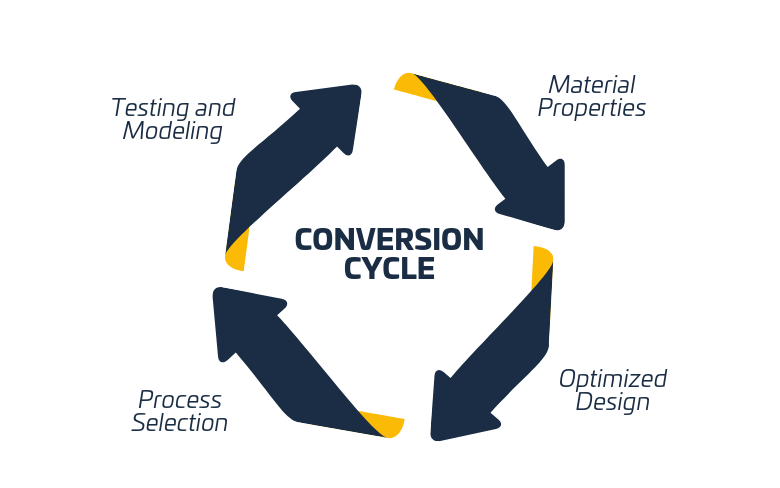
From powder to part, GKN Powder Metallurgy offers a full-service solution for any application challenge. Partnering from the concept stage, our experienced engineers design powder metal components to reduce weight and size, eliminate secondary machining and meet complex geometry requirements.
With extensive knowledge in powder from our business GKN Hoeganaes, advanced materials with strong capabilities are at our fingertips. Internally, we find the right manufacturing process for the product at a lower cost for serial production.
No knowledge in powder? No problem. GKN Powder Metallurgy is your ideal partner from concept and design to full production.
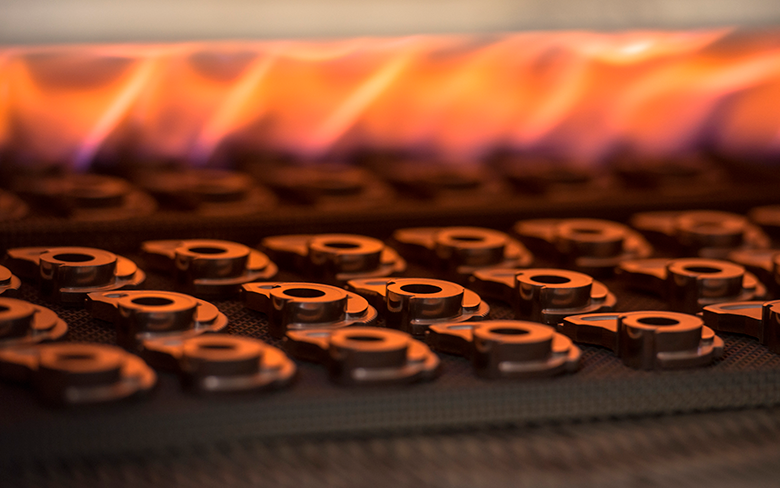
Powder metal is the ideal solution parts needing a complex geometry design, eliminating the need for machining. An example of this is with undercut technology, which presses the features during a specialized compaction process and eliminates the previous need for machining.
Our 2017 MPIF Grand Prize winning Output Pulley component showcases powder metal's ability to create a complex and net shape design. The part features a unique groove that was designed for PM production, providing full functionality as a net-shaped product. The application required a small footprint design with lightweight parts, resulting in the success of the compacted technology of the output pulley.
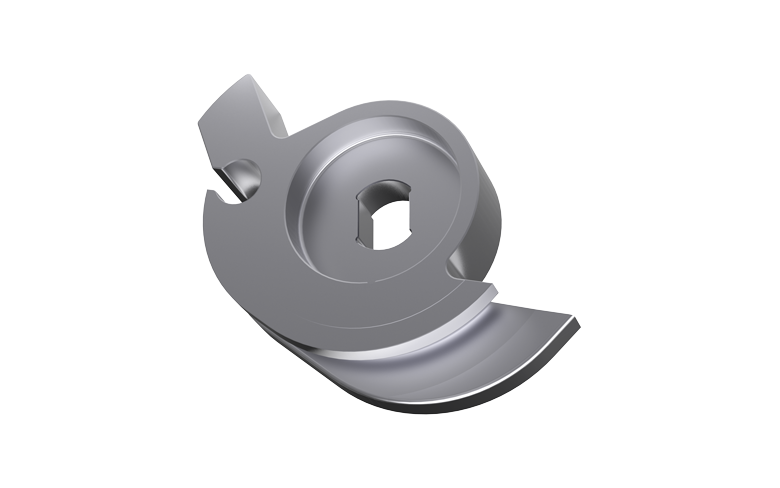
Requiring assembly operations and increasing product management, multi-component designs create additional design and machining challenges for engineers. With our Design for Powder Metal mentality, we create solutions to simplify assemblies.
Because of our longstanding experience in powder metal design, customers turn to us to find innovative solutions for multi-piece assemblies. Based on design and functionality requirements, we create multi-functional components with integrated designs and reduced operations. GKN Powder Metallurgy’s PM technology has the ability to develop and design a material, component or process to fit the needs of any customer.
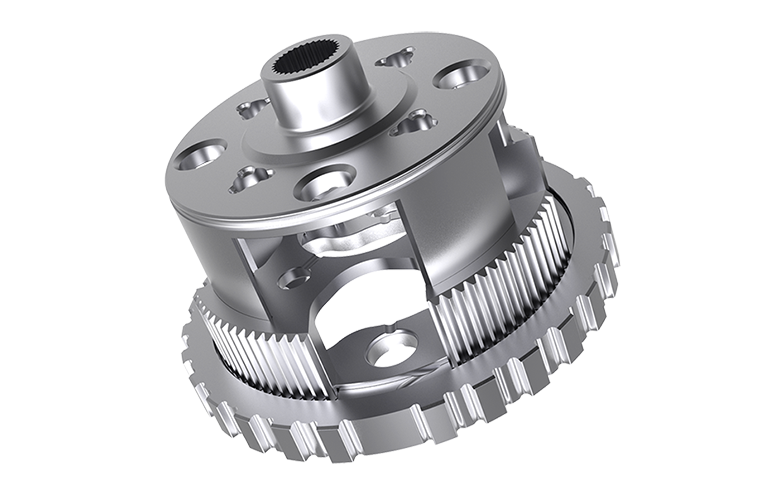
A crucial step in the production and testing process is Finite Element Analysis (FEA). The FEA process tests how the product performs under specific conditions, ensuring that the product meets all necessary requirements at all stages of production.
GKN Powder Metallurgy simulation capabilities:
- Structural FEA, thermal simulation and model analysis
- Fatigue life and fracture analysis
- Hot and cold forming, sizing and press fitting
- Induction heating and other special processing
- Product and process optimization
GKN Powder Metallurgy simulation advantages:
- Applied state-of-the-art CAE methods
- Integrated powder metal material monotonic and cyclic properties
- Access to fast and accurate simulations
- Augmented product performance
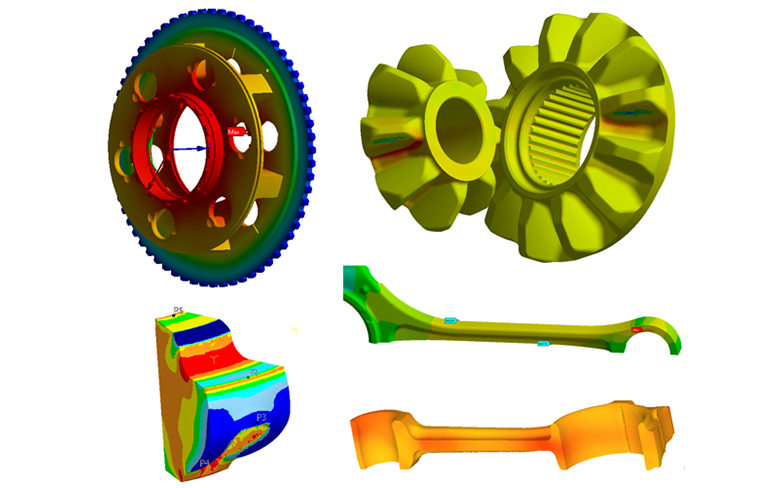
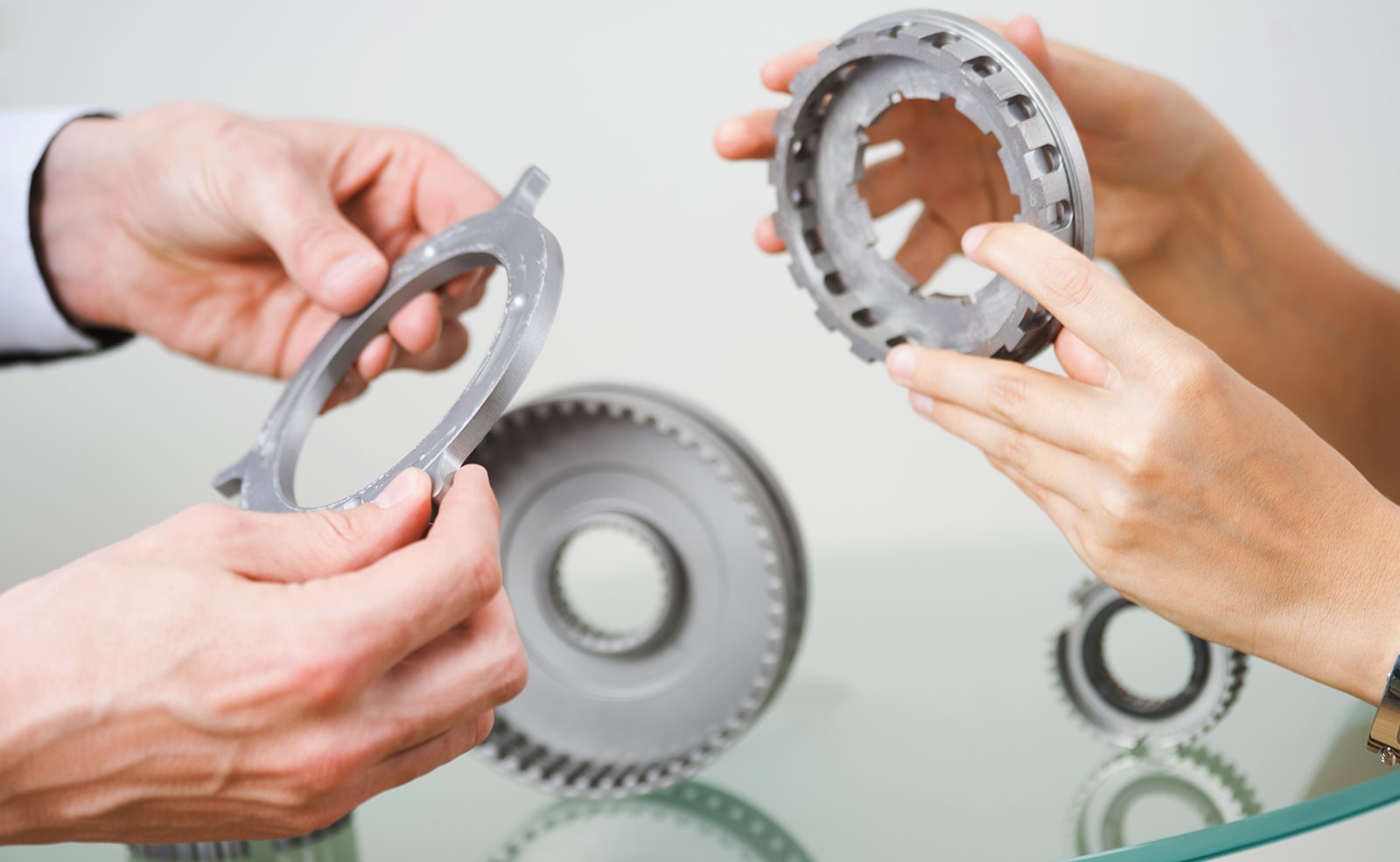
Markets
Overview
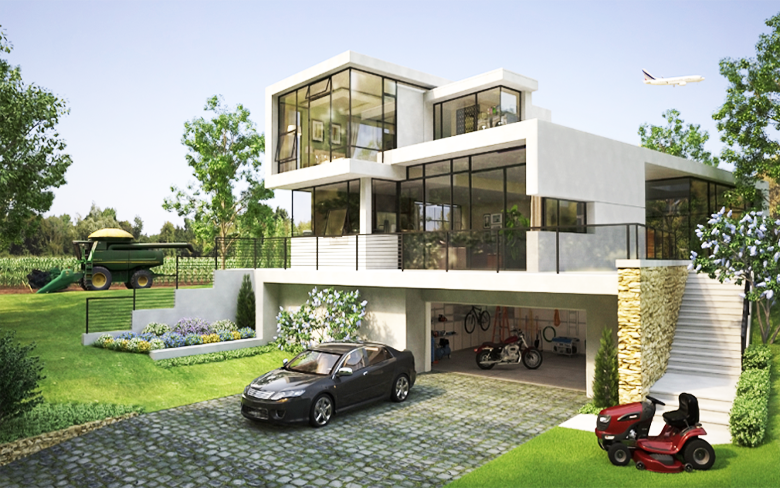
GKN Powder Metallurgy has taken its longstanding expertise in the automotive industry and has expanding the unparalleled advantages of powder metal into all markets outside of automotive. In terms of products, this can range from single-level components to complex designs with powder metal conversions.
Sub Markets
In the Compressors market, we produce the following components:
- Pistons
- Valve plates
- Bushings/bearings
- Scroll technology
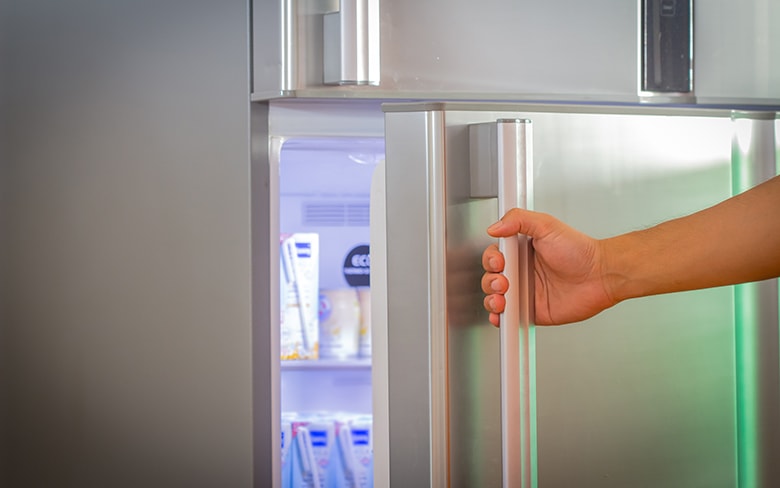
In the Household industry, we produce components for the following markets:
- Security
- Hardware
- Small kitchen appliances
- Waste disposal
- Faucets
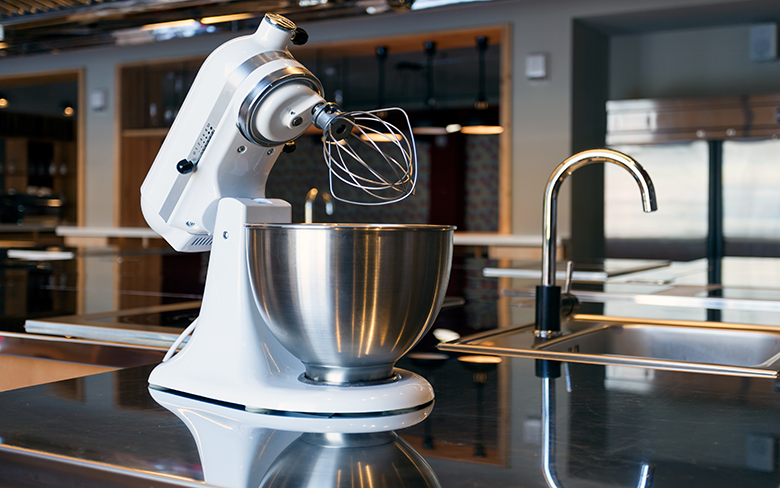
In the Off-road/RVS/Motorcycles markets, we produce the following components:
- Bushings/bearings
- Sprockets
- Suspension
- Valve train
- Gears
- Pulleys
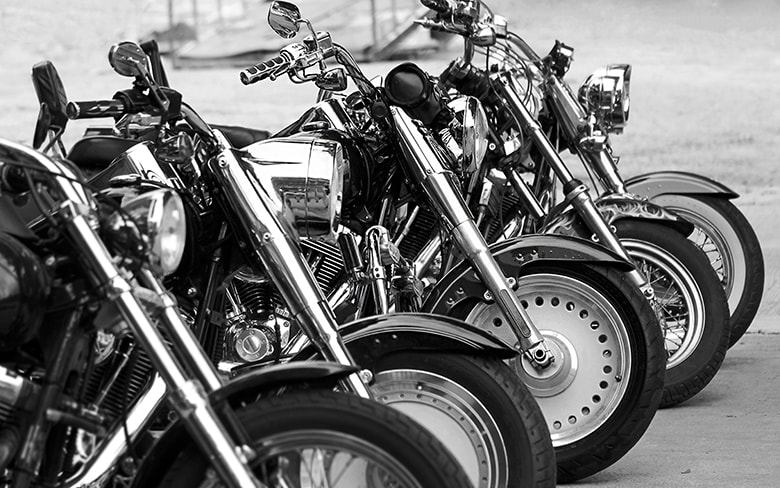
Every human body is different. This can make manufacturing in the medical industry difficult with custom and complex product solutions. Fortunately, powder metallurgy (PM), such as metal injection molding (MIM) and 3D metal printing (Additive Manufacturing) are the right fit for this growing market.
The medical industry requires materials that are human-body-compatible, non-corrosive, and have high wear resistance. With traditional processes, it can be difficult to make parts with these demands. However, MIM and 3D metal printing (Additive Manufacturing) are capable of producing intricate geometries and work with titanium, nickel alloys, surgical stainless steel, and more materials that work well inside the human body.
PM is supplying Pm components to the Medical market in the following ways:
- Structural supports: Artificial limbs, knee and hip joint replacements
- Surgical instruments: Forceps, graspers, knot pushers, and needle drivers
- Medical air compression: SMC eMotor components, value plates, pistons, connecting rods, bearings, and bushings
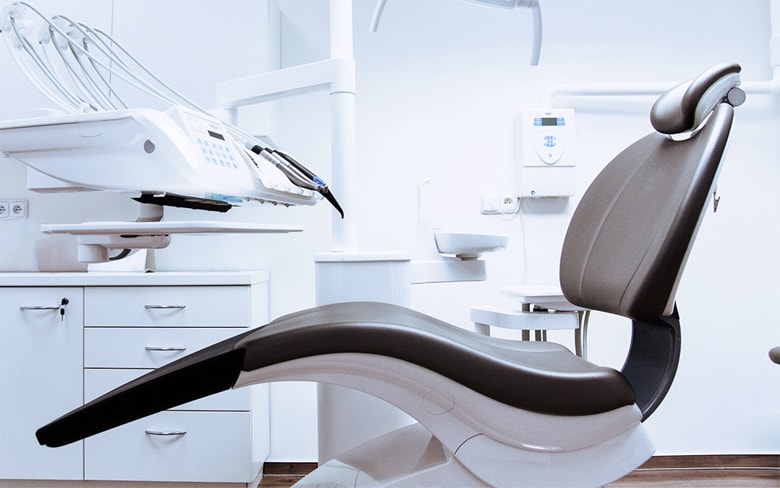
In the Lawn and Garden industry, we supply components for the following applications:
- Small engine
- Transmission - manual and hydrostatic
- General chassis
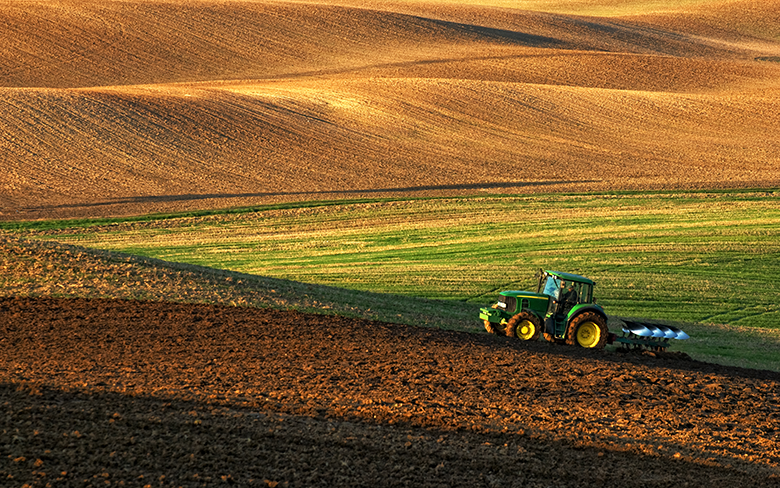
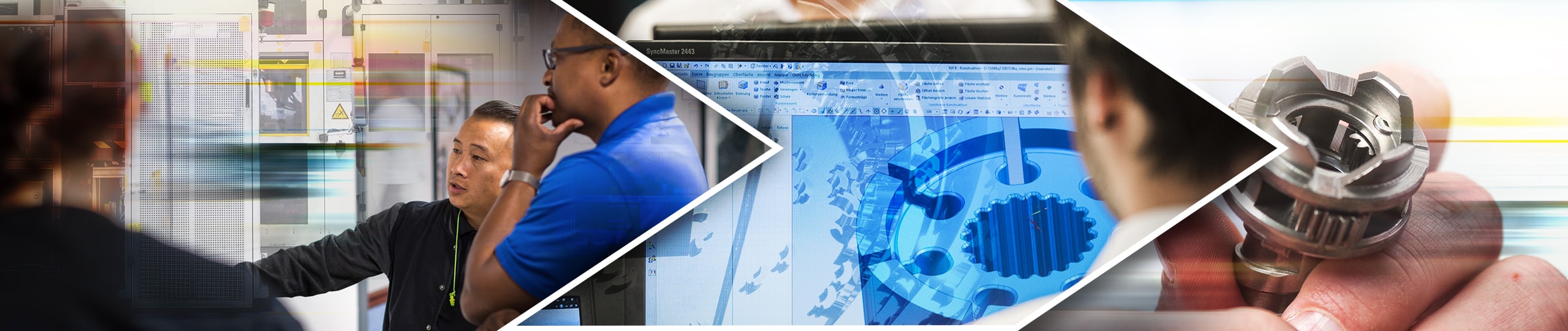
Technology
Overview
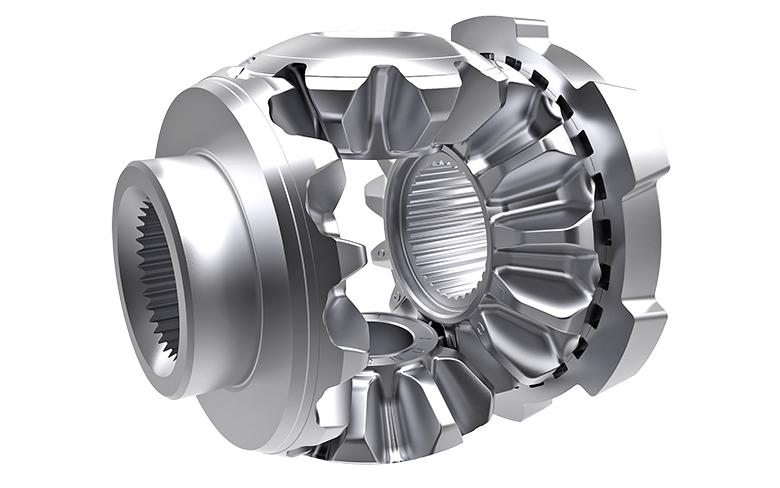
GKN Powder Metallurgy is world leader in the manufacturing of powder metal gears. For Industrial markets, we design and produce multiple forms of gearing technology, including:
- Helical gears
- Straight spur gears
- Bevel gears
- High performance powder forged gears
- Surface rolled densified gears
Gearing technology requires more than basic production, and that's what sets us apart. Our team of Industrial-dedicated engineers are equipped with exceptional in-house FEA analysis, inspection capabilities and cleanliness testing, just to start. Check back here soon, where we'll cover why GKN Powder Metallurgy is the preferred partner in Industrial gearing technology.